Control Charts are graphical tools used to monitor and control a process. There are different types of Control Charts, but all aim to help identify and correct process problems. Control charts can be used in many industries, such as healthcare, manufacturing, and as part of various methodologies such as TQM, Six Sigma, Kanban, and project management.
Control charts are used to study how a process changes over time and to identify when and how the process goes out of control. Control charts can help you to improve the quality of your product or service and to ensure that your process is running smoothly.
Control Charts is one of the 7 QC tools. Following are the other 7 QC Tools
Table of Contents
Who invented control charts?
The control chart was invented by Dr. Walter A Shewhart in the early 1920s.
Shewhart was working at Bell Laboratories at the time and was trying to find a way to improve the quality of telephone switches. Hence also called as Shewhart control charts.
Bell Laboratories was working on improving the reliability of its power transmission system. It was during this period Shewhart developed control charts.
Basics concepts for understanding Control charts
Understanding types of Variation
Control charts help us understand the type of variation in the process. There are two types of variations.
Common cause variation
Common cause variation is the variation that is inherent in the process and cannot be eliminated. It occurs when there is a change in the process, but the cause of the change is not known.
For example, common cause variation can occur when the temperature or humidity changes, when different operators work on the process, or when the machine is not in good working condition.
Special cause variation
Special cause variation is the variation that is not due to the common causes and can be eliminated. It occurs when there is a known or unknown cause of the change in the process.
For example, special cause variation can occur when an operator makes a mistake, when a machine breaks down, or when there is a change in the raw material.
Understanding type of Data
It is important to understand the types of data,since type of data is one of the important considerations for control chart selection.
Attribute data
Attribute data is data that is measured on a nominal or ordinal scale. Nominal data is data that is classified into categories, such as sex (male/female), race (white/black), or religion (Catholic/Protestant). Ordinal data is data that is ranked, such as first, second, third, etc.
Variable data
Variable data is data that is measured on a numerical scale. Variable data can be either continuous or discrete. Continuous data is data that can take any value within a certain range, such as height, weight, or temperature. Discrete data is data that can only take certain values, such as the number of defective items in a sample.
Types of Control Charts
In the previous section we understood two major concepts.
a. Control charts helps us understand the type of variation in the process and indeed help us understand if the process is stable or not.
It is important to note that we can conduct process capability only for stable processes.
b. Type of data is an important criteria for control chart selection and hence the control charts are divided according to the type of data analysed.
Based on the above argument there are two main types of control charts which are attribute control charts, and variable control charts.
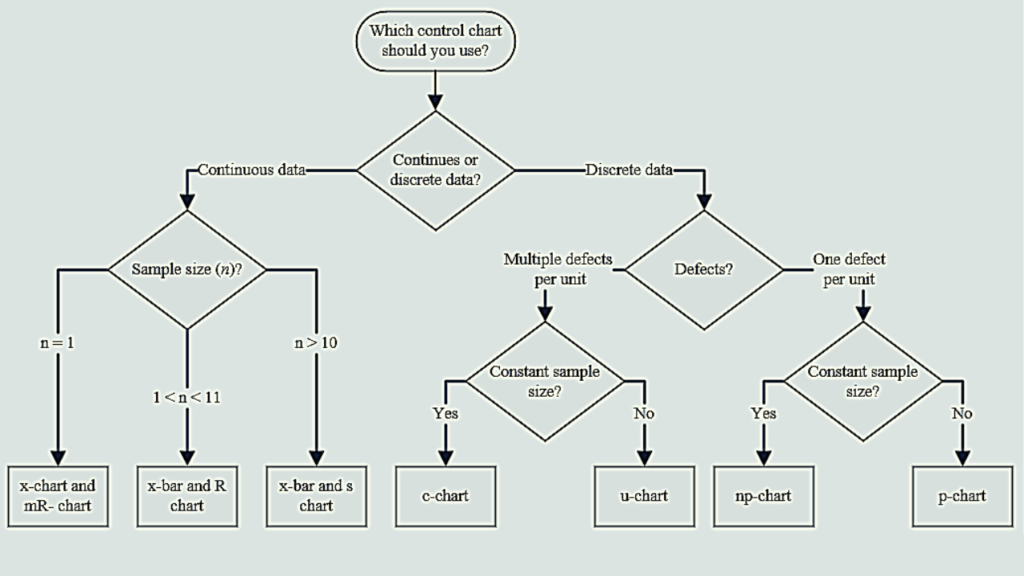
Attribute Control Charts
Attribute control charts are used with categorical data to control quality by monitoring the number or percentage of defective items produced or services performed. Common attribute control charts include:
P chart
- It tracks the percentage of defective items in a sample
- Used to monitor the percentage of defects in a process.
- A p-chart is an attributes control chart used with data collected in subgroups of varying sizes.
- Because the subgroup size can vary, it shows a proportion of nonconforming items rather than the actual count.
- P-charts show how the process changes over time. The process attribute (or characteristic) is always described in a yes/no, pass/fail, go/no go form.
Np chart
- It tracks the number of defective items in a sample.
- There are also np charts that are used to monitor the number of nonconforming items in a process. The np chart is used when the subgroup sizes are constant.
C chart
- It tracks the number of defects per unit
- Used to monitor the number of defects in a process.
- A c-chart is an attributes control chart used when the subgroup sizes are constant. The c-chart is used to monitor the number of defects in a process.
- The process attribute (or characteristic) is always described in a yes/no, pass/fail, go/no go form.
I chart
- Used to monitor the individual pieces produced in a process.
- The I-chart is used to monitor the number of pieces produced by a process.
- The I-chart is a variation of the c-chart and is used when the subgroup sizes are not constant.
U chart
- It tracks the average number of defects per unit
- Used to monitor the under-run and over-run of a process.
- The u-chart is used to monitor the difference between the desired and actual production quantity for a process. The u-chart helps you to determine whether your process is stable or not.
Variable control charts
Variable control charts are used with continuous data to control quality by monitoring the mean and variation of a process. Common variable control charts include:
X bar and R chart
- Used to monitor the mean and range of a process. X bar charts are used for comparing the average values of samples collected over time.
- An individual x bar chart can be created by plugging the result of each sample into the chart.
- R charts are used to monitor the variability of the samples.
X bar and S chart
- X bar and s chart tracks the mean and variation of a processAn S-chart is a type of control chart used to monitor the standard deviation of a process.
- Each point on the chart represents the value of a subgroup standard deviation.
- The expected value of the standard deviation statistic is the centerline for each subgroup. The centerline varies when the group sizes are unequal.
Why Use Control Charts?
There are many reasons why you might want to use a control chart, including the following:
- To improve the quality of your product or service.
- To ensure that your process is running smoothly.
- To identify and correct process problems.
- To study how a process changes over time.
- To determine when and how the process goes out of control.
- To learn how to interpret control charts.
- To determine the limits for a control chart.
- To have a software tool to help you with your control charting.
- To be able to use control charts in conjuction with various methodologies such as 8D,DMAIC,Kanban,Kaizen,etc.
What are the benefits of using control charts?
There are many benefits to using control charts, including:
- they help to identify problems in a process
- they help to determine the cause of the problem
- they help to find the appropriate corrective action
- they help to track the progress of the corrective action
- they help to prevent future problems.
How is control chart data collected?
The control chart data is usually collected by taking a sample of the process at regular intervals. The samples are then analyzed to see how they compare to the control limits. If the data falls outside of the control limits, it indicates that a problem has been detected in the process.
8 Rules for Control Chart interpretation
Rule | Rule Name | Pattern |
1 | Beyond Limits | One or more points beyond the control limits |
2 | Zone A | 2 out of 3 consecutive points in Zone A or beyond |
3 | Zone B | 4 out of 5 consecutive points in Zone B or beyond |
4 | Zone C | 7 or more consecutive points on one side of the average (in Zone C or beyond) |
5 | Trend | 7 consecutive points trending up or trending down |
6 | Mixture | 8 consecutive points with no points in Zone C |
7 | Stratification | 15 consecutive points in Zone C |
8 | Over-control | 14 consecutive points alternating up and down |
Advantages and Disadvantages of Control Charts
Advantages of Control Charts
There are many advantages to using control charts, including the following:
- They can help you to identify and correct process problems.
- They can improve the quality of your product or service.
- They can ensure that your process is running smoothly.
- They can be used in many industries, such as healthcare, manufacturing, TQM, Six Sigma, kanban, and project management.
Disadvantages of Control Charts
There are also some disadvantages to using control charts, including the following:
- It can be time consuming and expensive to set up a control chart.
- It can be difficult to interpret control charts.
- The rules for control charts can be complex.
- Control charts can be inaccurate if the process is not stable.
Applications/Uses
How to use control charts in Six Sigma methodelogy?
Control charts are used in DMAIC’s six sigma methodology to identify and correct process problems.
Control charts can be used to identify which type of variation is present in a process. Once the type of variation is identified, the appropriate corrective action can be taken.
Control Charts are used in measure and analyse phase of DMAIC.Control Charts help you determine whether your process is stable or not.
Control chart is used to distinguish between the types of variation.
How control charts are used in healthcare?
In healthcare, control charts are used to monitor various aspects of patient care, such as blood pressure, heart rate, and oxygen levels.
- Control charts can also be used to monitor the performance of medical staff, such as
- Control charts are used to monitor the quality of a medical staff
- Control charts can be used to identify the type of variation present in a process
- Control charts enable you to take corrective action when problems arise.
Medical field has very low margins for error,hence control charts are a necessity for quality control. Any mistake in the process can have serious consequences for the patient. Control charts help to identify and correct any process problems before they can cause harm to the patient.
Moreover, hospitals are aspiring for better and better services and control charts helps improve the quality of care that they provide. Control charts help to identify and correct any process problems before they can cause harm to the patient. This enables hospitals to provide the best possible care for their patients.
How control charts are used in Manufacturing?
In manufacturing, control charts are used to monitor the quality of the product. Control charts can be used to identify the type of variation present in a process and to take corrective action when problems arise.
Control charts are an important tool for ensuring the quality of the product. They help to identify and correct any process problems before they can cause harm to the customer.
Manufacturers are constantly looking for ways to improve the quality of their goods. Control charts are an important instrument for reaching this goal.
In manufacturing control charts are used as a part of many methodologies such as
- TQM
- KANBAN
- DMAIC
- 8D
- Process Capability Analysis
How control charts are used in the Service Industry?
In the service industry, control charts are used to monitor various aspects of the service provided. Control charts can be used to monitor following aspects in service industry
- the quality of the service
- the performance of the staff
- the satisfaction of the customer.
Control charts are used in service businesses and since service businesses have such narrow margins for error, control charts are required for quality assurance. Any slipup in the procedure may have serious consequences for the client.
Control charts assist to detect and correct any process issues before they can cause harm to the client.
Important Points to remember when using control charts
- Control charts should be used with a subgroup size of at least five
- Control charts should be used with a data sample that is representative of the process
- Control charts should be used to monitor only one process variable at a time
- Control charts should be updated at regular intervals
- Control charts should be used in conjunction with other quality control tools.
- Control charts are only as good as the data that they are based on.
- Control charts are not a substitute for sound engineering judgment.