Table of Contents
Definition
PPAP stands for Production Part Approval Process. It’s a standardized set of requirements designed to instill confidence in a supplier’s production process.
PPAP was initially used in automotive and aerospace industries but nowadays it is being widely used in other industries as well.
Nowadays considering manufacturing complexity all components can’t be made in-house and hence has to be outsourced to the sources available in domestic as well as international markets. Maintaining product quality in such a scenario becomes altogether more difficult.PPAP comes to the rescue here.
Since PPAP is a standardized set of requirements, it clearly communicates customer requirements to the suppliers, and based on whether the requirements are met or not, the customer could approve or reject the part or the process. This approval process ensures part quality is as per customer expectations.
The PPAP process consists of 18 elements required for the approval of production-level parts. There are multiple types of submission and all elements are not required for all the submissions. There are five levels of PPAP submission, each with different submission requirements.
The PPAP guidelines are published by AIAG. Currently, the 4th edition of the PPAP manual is in supply.
The submission provides assurance that the supplier has met or exceeded the customer’s requirements and the process is capable of consistently producing quality parts.
Origin of PPAP
PPAP, the Production part approval process, was developed by AIAG, Automotive Industry Action Group, in 1993.
At that time each Auto giant had a different set of requirements, but most of their suppliers were common. So it became very frustrating for the supplier to maintain and present data in different forms and formats as per each OEM requirement.
The big three auto giants at that time, Ford, GM, Chrysler realized this issue and this realization led to the genesis of PPAP and other core tools.
The latest issue of the PPAP manual published by AIAG is the 4th edition. Issued in 2006.
Since 1993, the Production Part Approval Process has expanded into many other industries including aerospace, agricultural, commercial, and food & beverage manufacturing.
What is the purpose of PPAP?
The purpose of PPAP is as follows
- To determine if all customer engineering design records and specification requirements are properly understood by the Suppliers.
- The manufacturing process has the capability to produce products consistently meeting these requirements during an actual production run at the quoted production rates.
- Provides objective evidence that the supplier meets all customer-specific requirements.
In short, PPAP provides confirmation that the customer and supplier are on the same page in regards to the understanding of engineering design specifications and requirements.
What are the five levels of PPAP Submission?
The PPAP submission requirements are divided into five levels based on the submission requirements, as follows:
- Level 1 – Part Submission Warrant (PSW) or AAR(if required) only submitted to the customer(Applicable for non-Critical parts or Aesthetic parts)
- Level 2 – PSW with product samples and limited supporting data(Applicable for bulk material like paint, plastics, special fasteners)
- Level 3 – PSW with product samples and complete supporting data(It is the default level used throughout the industry)
- Level 4 – PSW and other requirements as defined by the customer
- Level 5 – PSW with product samples and complete supporting data available for review at the supplier’s manufacturing location(Generally for Safety-Critical Products)
Note :
- It is important to understand that the PPAP submission level is at the discretion of the customer. AIAG manual provides only general guidelines as to which level to use in a given situation.
- Regardless of the submission level, the supplier is obligated to complete all of the applicable elements and retain the ones that aren’t submitted.
- PPAP level pertains only to what’s submitted, not to what’s actually performed.
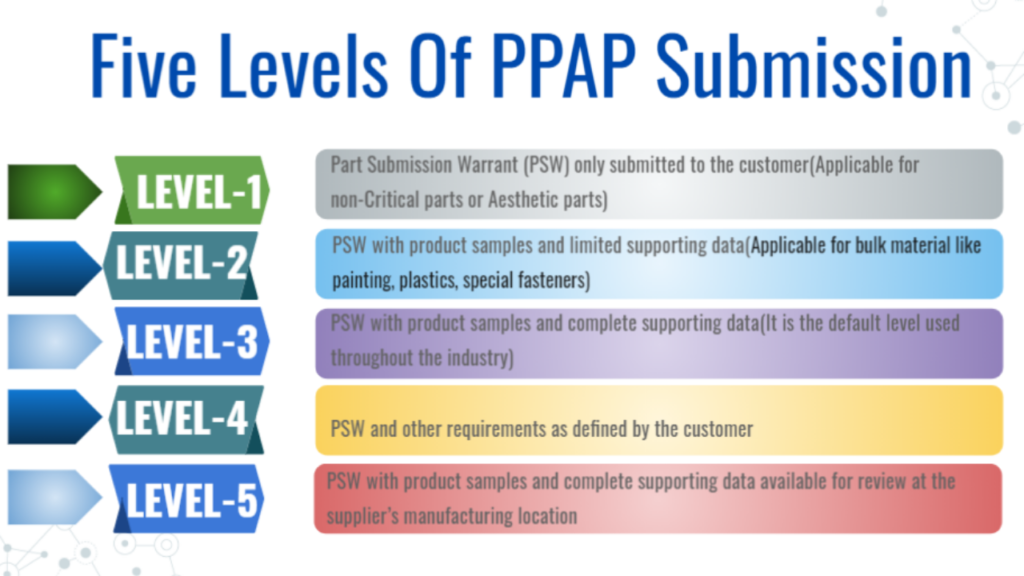
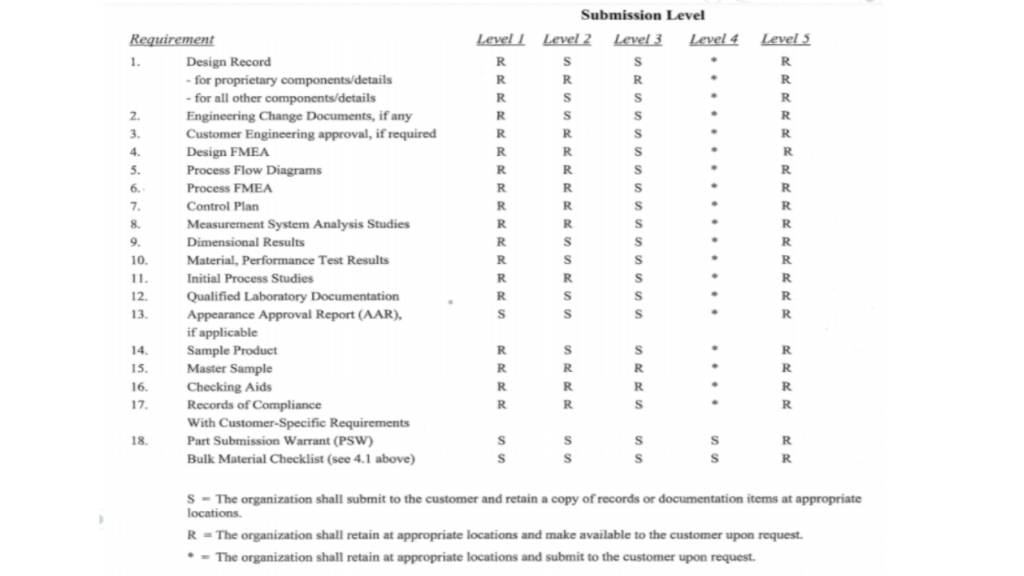
What are the 18 elements of PPAP?
Design Records
- Design records include Customer provided product drawing, Internal drawing of supplier, purchase order, and Product sample in some cases.
- In case the product is designed by the supplier the drawing is prepared by the supplier and approved by the customer.
- Each and every feature must be “ballooned” or “road mapped” to correspond with the inspection results (including print notes, standard tolerance notes and specifications, and anything else relevant to the design of the part).
- Design records ensure that customers and suppliers are discussing the same part and with the same revision level.
Authorized Engineering Change Documents
- The supplier shall provide authorized change documents for those changes not yet recorded in the design record, but incorporated in the product, part, or tooling.
Engineering Approval
- Suppliers shall have evidence of customer engineering department approvals, wherever applicable.
- This approval is usually the Engineering trial with production parts performed at the customer plant.
- Production parts are sent to the customer’s engineering department along with temporary deviation and the customer’s engineering department performs testing and provides approval.
Design Failure Mode and Effects Analysis (DFMEA)
- DFMEA(Design failure mode and effects analysis) is a form of failure mode and effects analysis performed at the design stage.
- DFMEA is a cross-functional team activity.
- This activity includes the examination of design risks by exploring the possible failure modes and their effects on the product or customer and their probability to occur.
- This activity is conducted before completing a design and uses information generated in this activity to mitigate the causes of various potential failures.
- Since DFMEA is conducted at the design stage, DFMEA shall be conducted by either customer or supplier depending on who designed the product.
- If DFMEA is conducted by a part supplier, a copy of DFMEA, reviewed and signed by customer and supplier, shall be made available as per submission level.
- The DFMEA is a living document that should be reviewed and updated throughout the product life cycle.
Process Flow Diagrams
PFD is a visual diagram of the entire process from receiving through shipping, including outside processes and services.
Purpose of PFD is to help people visualize the real process. Process maps can be used to understand the following characteristics of a process:
• Step-by-step process linkage
• Offline activities (measurement, inspection, handling)
Checklist to validate PFD
- Process Flow must identify each step in the process
- Should include abnormal handling processes such as Scrap,Rework.
- Process Flow must include all phases of the process such as ,Receiving of raw material,Part manufacturing,Offline inspections and checks,Assembly,Shipping.
Process Failure Mode and Effects Analysis (PFMEA)
- PFMEA(Process failure mode and effects analysis) is a form of failure mode and effects analysis performed at the process designing stage.
- PFMEA similar to DFMEA is a cross-functional team activity. This activity includes examination of risks by exploring the possible failure modes and their effects on the product or customer and their probability to occur.
- This activity is conducted after completion of the process flow diagram and prior to tooling for production.
- PFMEA is a tool used to identify and prioritize risk areas and design their mitigation plans
- A copy of PFMEA, reviewed and signed by customer and supplier, shall be made available as per submission level.
- The PFMEA is also a living document that should be reviewed and updated throughout the product life cycle.
Checklist for good PFMEA
- Make sure that all critical failure modes are addressed,such as Safety,Form, fit, function, Material concerns,etc.
- Make sure that high RPN process concerns are carried over into the control plan
- Make sure all processes are covered.
- All past troubles are taken into consideration.
Control plan
- A control plan is a document that describes how to control the critical inputs to continue to meet customer expectations of the output.
- The control plan acts as the primary reference source for minimizing process and product variation.
- The control plan also includes a description of how teams should react to out-of-control situations.
- PFMEA acts as input for the control plan.
Checklist for Control Plan
- Use process flow diagram and PFMEA to build the control plan; keep them aligned
- Controls must be used to be effective. Keep it simple.
- Ensure that the control plan is in the document control system of the business
- Good control plans address: All testing requirements – dimensional, material, and performance,All product and process characteristics at every step throughout the process.
- The control method should be based on effective analysis of the process Such as SPC, Error Proofing, Inspection, Sampling Plan
- Control plans should reference other documentation Ex. Specifications, tooling, etc.
Measurement System Analysis Studies (MSA)
- An MSA is a statistical tool used to determine if a measurement system is capable of precise measurement.
- MSA helps determine how much error is in the measurement due to the measurement process itself.MSA quantifies the variability added by the measurement system.
- It is important for suppliers to conduct MSA to make sure the supplier’s measurement system is within acceptable measurement variation.
Dimensional Results
- A dimensional layout of sample parts is required to validate the product meets the customer’s required specifications. It acts as evidence that dimensional verifications have been completed and results indicate compliance with specified requirements.
- Parts are randomly selected from the complete lot and are checked as per all product and process specifications. Based on observations results are categorized as “OK” or “NOT OK”.
- Layout reports usually include results from 5 to 6 parts. It is important to note that this is a sample size for layout inspection but not to perform statistical process control.
Records of Material / Performance Tests
- This includes a summary of all validation tests performed on the part. It is in the form of a Design Verification Plan and Report (DVP&R).DVP&R lists each and every test performed, a description of how the test was performed, and the results of each test.
- The supplier shall perform tests for all parts and product materials when chemical, physical, or metallurgical requirements are specified by the design record or Control Plan.
- Also, the supplier shall perform tests for all parts or product materials when performance or functional requirements are specified by the design record or Control Plan
Initial Process Studies
Initial process studies include statistical process control conducted on critical characteristics of the product. These studies demonstrate that the critical processes are stable, demonstrate normal variation, and are running near the intended nominal value.
It helps determine if the production process is likely to produce product that will meet customer requirements.
Checklist for SPC
Ensure that the results are acceptable and that the process is stable and capable of producing a quality part
PPAPs should only be approved if the capability is greater than 1.67 for critical dimensions and greater than 1.33 for non-critical dimensions
Qualified Laboratory Documentation
- Inspection and testing for PPAP shall be performed by a qualified laboratory.
- The qualified laboratory (internal or external to the supplier) shall have a laboratory scope and documentation showing that the laboratory is qualified for the type of measurements or tests conducted
- When an external laboratory is used, the supplier shall submit the test results on the laboratory letterhead or the normal laboratory report format.
Appearance Approval Report (AAR)
The Appearance Approval Inspection (AAI) is applicable for parts affecting appearance only. This report demonstrates that the part has met the appearance requirements on the design record. The appearance requirements could include information regarding the color, surface finish, etc.
Sample Product Parts
These are actual samples that reflect the parts documented in the PPAP. The sample parts provided should be the same parts measured for the dimensional results. The default quantity for all submissions is 5 parts unless otherwise requested.
Sample production parts MUST be properly identified. Include the following information on the part label:
- Date parts were packed
- Part number
- Quantity
- Serial number
- Supplier part number (optional)
- Part description
- Country of origin
Sample production parts are typically stored at either the customer or supplier’s site after the product development is complete.
Master Sample
A master sample is a final sample of the product that is inspected and signed off by the customer. The master sample part is used to train operators and serves as a benchmark for comparison to standard production parts if any part quality questions arise
Checking Aids
- This includes detailed list of all the checking aids used for production.Checking aids may include check fixtures, contour, variable and attribute gages, models or templates.
- This list shall include calibration schedule for the listed checking aids.
- MSA may have to be conducted for these aids based on customer requirement.
Customer-Specific Requirements
This element contains supporting documents for any of the customers specified requirements, not covered in these 18 points.
Part Submission Warrant (PSW)
The Part Submission Warrant (PSW) form is a summary of the entire PPAP submission.PSW is required for all levels of PPAP submission.
PSW includes :
- Change level(Reason for PPAP)
- Drawing numbers and revisions
- Level of PPAP submission
- Declaration of conformance to customer requirements.
- Tool details such as no. of cavities.
- Customer Approval.
What are the PPAP Approval Status types?
Approved
Approved indicates that the part or material, including all sub-components, meets all customer requirements. The organization is therefore authorized to ship production quantities of the product, subject to releases from customer scheduling activity.
Interim Approval
Interim approval allows for shipment of material for production requirements on a limited time or piece quantity basis.
- Clearly defined non-compliance.
- Action Plan Agreed upon by Customer.
- Low Volume Parts
Rejected
When PPAP Submission does not meet customer expectations.
When to perform PPAP?
PPAP is generally submitted for following situations. But this list is not exclusive,PPAP might have to be submitted based on customer requirement.
- New part
- Engineering change(s)
- Tooling: transfer, replacement, refurbishment, or additional
- Correction of discrepancy
- Tooling inactive > one year
- Change to optional construction or material
- Sub-supplier or material source change
- Change in part processing
- Parts produced at a new or additional location
What are the benefits of PPAP?
- Helps to maintain design integrity
- Identifies issues early for resolution
- Reduces warranty charges and prevents the cost of poor quality
- Assists with managing supplier changes
- Prevents use of unapproved and nonconforming parts
- Identifies suppliers that need more development•Improves the overall quality of the product & customer satisfaction
Very Useful Context.
Thank-You!
Attractive section of content. I just stumbled upon your web site and in accession capital to
assert that I acquire in fact enjoyed account your blog posts.
Anyway I’ll be subscribing to your feeds and
even I achievement you access consistently fast.
I together with my pals appeared to be taking note of the nice items located on the blog while immediately developed a terrible feeling I never thanked the web blog owner for those secrets. The boys are already for that reason passionate to learn them and have now undoubtedly been using those things. I appreciate you for really being simply thoughtful and then for choosing this sort of magnificent tips millions of individuals are really wanting to understand about. My personal honest regret for not expressing appreciation to you sooner.
I抣l right away grab your rss feed as I can’t find your email subscription link or newsletter service. Do you’ve any? Please let me know so that I could subscribe. Thanks.
Fantastic site. A lot of useful information here. I am sending it to a few friends ans also sharing in delicious. And obviously, thanks for your sweat!