In recent years, Industry 4.0 has been revolutionizing the manufacturing industry by introducing advanced technologies such as IoT, AI, and automation. At the same time, Lean Manufacturing has been gaining popularity as a methodology for improving efficiency, reducing waste, and increasing productivity in manufacturing processes.
The purpose of this blog is to explore the impact of Industry 4.0 on Lean Manufacturing, and how the integration of advanced technologies can enhance the effectiveness of lean manufacturing principles. We will look at the benefits and challenges of implementing Industry 4.0 in a lean manufacturing environment, and provide real-world examples of companies that have successfully integrated these technologies.
The blog will also offer recommendations for businesses looking to implement Industry 4.0 in their own lean manufacturing processes.
Table of Contents
Industry 4.0
Industry 4.0 refers to the fourth industrial revolution, characterized by the integration of advanced technologies such as IoT, AI, and automation into manufacturing processes. It aims to create a smart and connected industry, where machines can communicate and collaborate with each other to improve efficiency and productivity.
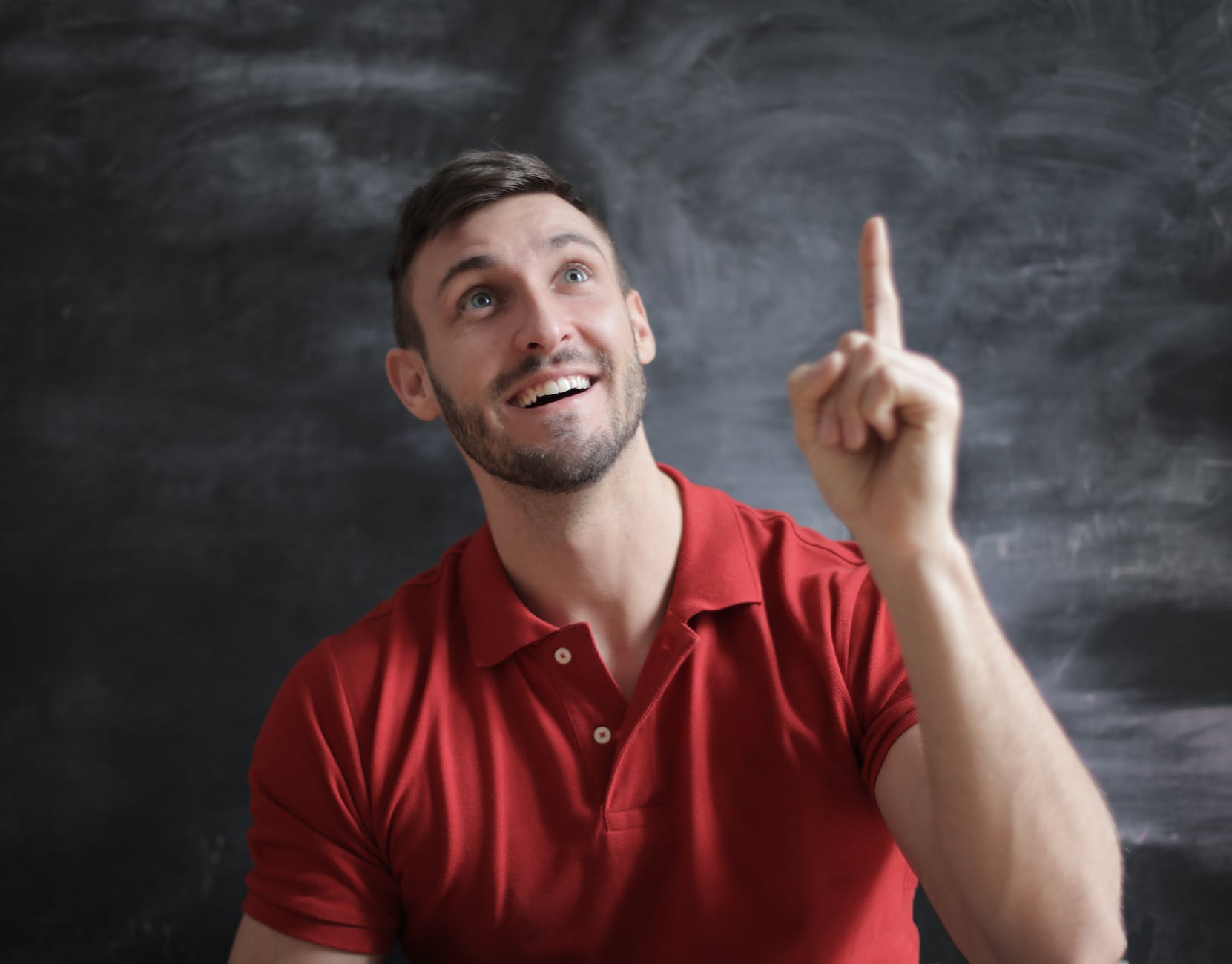
Lean Manufacturing
Lean Manufacturing is a methodology that aims to eliminate waste and improve efficiency in manufacturing processes. It focuses on maximizing value for customers while minimizing waste, through the use of principles such as continuous improvement and the elimination of non-value-adding activities.
The key principles of Lean Manufacturing include
- Identifying and eliminating waste
- Continuously improving processes
- Focusing on flow and pull systems
- Empowering employees
- Building a culture of continuous improvement
- Pursuing perfection
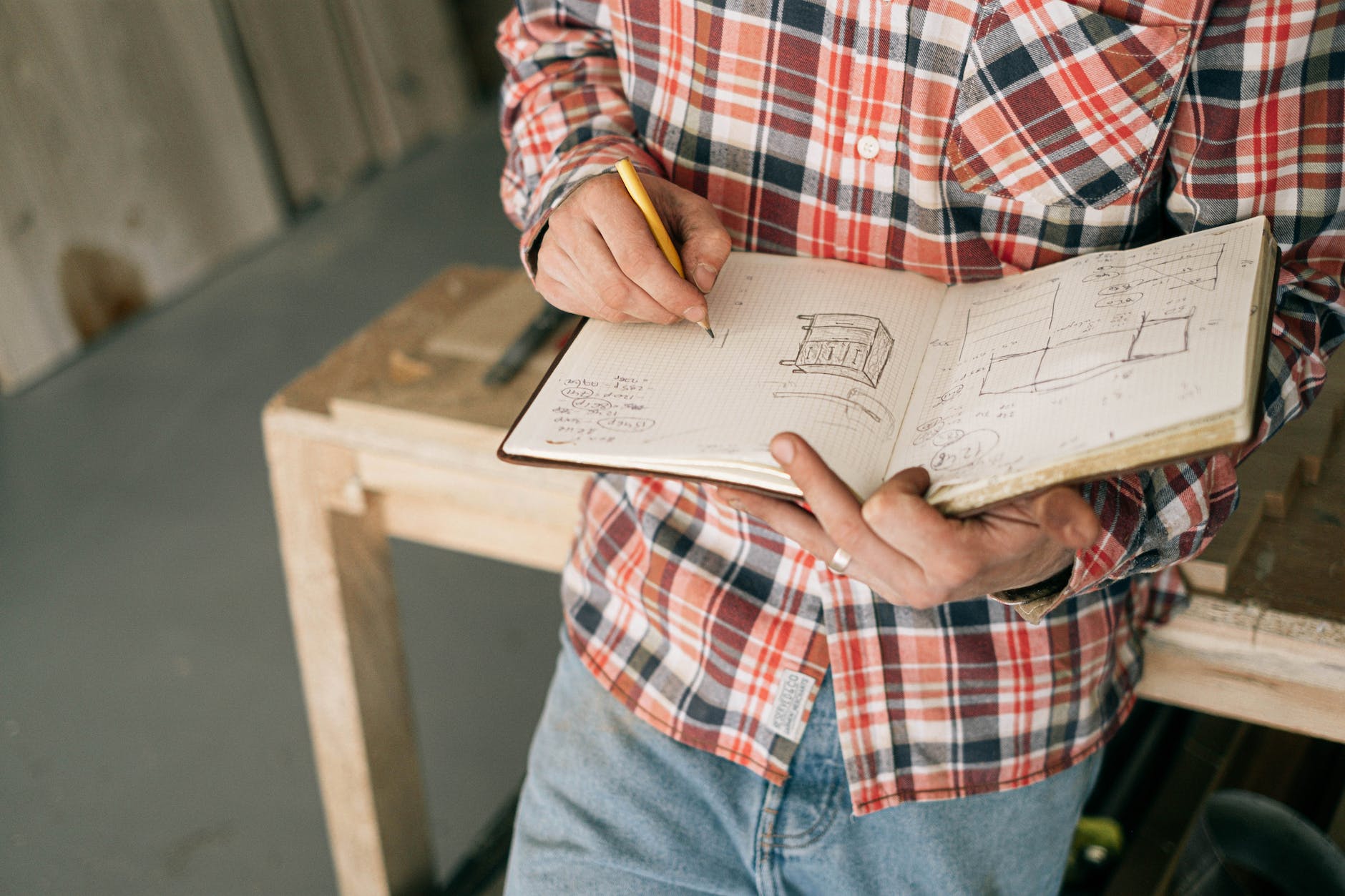
Examples of Lean Manufacturing in action
- Toyota Production System: Toyota’s approach to manufacturing, known as the Toyota Production System, is widely considered to be the birthplace of lean manufacturing.
- Boeing: Boeing’s lean manufacturing initiatives have led to significant cost savings and improved efficiency in their production processes.
- Dell: Dell’s lean manufacturing approach, known as “Dell Direct,” allows customers to customize and order their computers online, which has greatly improved the company’s efficiency and responsiveness to customer demand.
- P&G: Procter & Gamble has implemented lean manufacturing principles in their production processes, leading to significant cost savings and improved product quality.
These are just a few examples, but lean manufacturing is widely used in many sectors and many companies have implemented it in their operations.
The Impact of Industry 4.0 on Lean Manufacturing
A. Increased automation and data collection
Industry 4.0 technologies such as IoT, AI, and automation can greatly increase the level of automation in manufacturing processes. This can lead to improved efficiency and reduced waste, as well as increased data collection and analysis capabilities, which can support continuous improvement efforts.
B. Improved visibility and traceability
The use of Industry 4.0 technologies such as RFID and IoT can greatly improve visibility and traceability in manufacturing processes. This can help identify bottlenecks and inefficiencies, as well as improve product quality and reduce the risk of defects.
C. Enhanced decision-making capabilities
Industry 4.0 technologies such as big data analytics and AI can greatly enhance decision-making capabilities in manufacturing processes. This can support the identification of inefficiencies, the optimization of production processes, and the prediction of future demand.
D. Increased efficiency and reduced waste
The integration of Industry 4.0 technologies into manufacturing processes can lead to increased efficiency and reduced waste. This can be achieved through the elimination of non-value-adding activities, the optimization of production processes, and the reduction of defects and rework.
E. Challenges and considerations for implementing Industry 4.0 in a lean manufacturing environment
Implementing Industry 4.0 in a lean manufacturing environment can present a number of challenges and considerations, such as:
- Ensuring the compatibility of Industry 4.0 technologies with existing systems
- Addressing data security and privacy concerns
- Addressing the need for new skills and training for employees
- Addressing the potential for increased complexity in manufacturing processes
- Managing the significant costs associated with the implementation of Industry 4.0 technologies
These are some of the challenges and considerations that companies need to take into account when implementing Industry 4.0 in their lean manufacturing environment.
Case studies
A. Real-world examples of companies implementing Industry 4.0 in their lean manufacturing processes:
- Siemens: Siemens has implemented Industry 4.0 technologies in its manufacturing processes, leading to improved efficiency, reduced waste, and increased flexibility in production.
- GE Appliances: GE Appliances has implemented Industry 4.0 technologies in its manufacturing processes, resulting in improved efficiency, reduced waste, and increased productivity.
- Bosch: Bosch has implemented Industry 4.0 technologies in its manufacturing processes, resulting in improved efficiency, reduced waste, and increased customization capabilities.
The implementation of Industry 4.0 in these companies’ manufacturing processes has led to a number of benefits, including improved efficiency, reduced waste, increased productivity, and increased customization capabilities.
These companies have also been able to improve their ability to respond to changing customer demand, and have seen a significant reduction in costs.
Summary of key points
Industry 4.0 can greatly enhance the effectiveness of lean manufacturing principles, through the integration of advanced technologies such as IoT, AI, and automation. The implementation of Industry 4.0 in a lean manufacturing environment can lead to increased efficiency, reduced waste, improved visibility, and enhanced decision-making capabilities. However, companies need to consider the compatibility of Industry 4.0 technologies with existing systems, data security and privacy concerns, the need for new skills and training for employees, the potential for increased complexity in manufacturing processes, and the significant costs associated with implementation.
As Industry 4.0 continues to evolve, it is likely that we will see even more advanced technologies being integrated into manufacturing processes. This will likely lead to even greater improvements in efficiency, productivity, and customization capabilities. However, it will also likely lead to new challenges and considerations for companies looking to implement Industry 4.0 in their manufacturing processes.
Businesses looking to implement Industry 4.0 in their lean manufacturing processes should carefully consider the compatibility of Industry 4.0 technologies with existing systems, data security and privacy concerns, the need for new skills and training for employees, the potential for increased complexity in manufacturing processes, and the significant costs associated with implementation. They should also look for opportunities to collaborate with other companies and organizations to share best practices and expertise.